关键词 :汽车车门内装饰;产品微发泡;气体反压工艺期刊论文发表
随着汽车技术的发展,以及汽车产品自身结构功能的日益丰富与完善,人们对产品质量以及节能、环保、安全等方面的标准要求也在逐步提升,这就需要技术的进步为生产工作的顺利开展提供支撑。
1. 微发泡工艺简介
1.1 工艺分类
发泡工艺是指在塑料中加入一定比例的化学发泡剂,用注塑机融化塑料后注入模具中,发泡剂由于受到模具的约束在模具内产生作用,从而获得表面呈出韧结皮状而内部有气孔的塑料制件。物理发泡工艺是指注入超临界N2或者二氧化碳,再将混合形成的扩散溶液注入型腔中。随着注入过程中压力与热力学不稳定性的不断变化,会产生出大量的气泡核,气泡在冷却与填充的过程中逐渐变大和固定,就形成了微孔发泡制品。
1.2 发泡原理
当泡沫塑料内部裂纹尺寸大于塑料泡孔时,泡孔不但不会降低材料的机械性能,还会使材料存在的裂纹尖端出现钝化,抑制裂纹在应力作用下的进一步发展趋势,相应的材料性能反而得到提升,这体现出了微孔塑料设计思想。聚合物微孔发泡成型需要经历以下几个步骤,分别是聚合物或气体均相体系形成、泡孔成核、长大和定型。不但过程复杂,而且成型机理存在差异,影响因素也不尽相同。聚合物或均相体系形成对泡孔核的形成、长大和定型都产生影响,是发泡过程的必要条件。气泡核的形成会影响气泡核分布与孔密度;气泡形状会影响气泡的形状与结构;气泡定型会对气泡长大的结果能否长久保持产生影响。
1.3 微发泡优势
产品内部的发泡程度不同,能够节约的材料也就不同。微发泡的优势主要体现在质量能够降低质量。
1.3.1 微发泡会使产品的机械性能得到提升,消除制件的残余应力,避免下陷或翘曲的情况。
1.3.2 微发泡可以使气泡压力均匀分布,从而使模腔内部容积与模壁之间能够形成有效贴合。
1.3.3 由于尺寸稳定避免了重复修改,使设计成本得到有效控制,从而降低了制造成本。
1.3.4 微发泡能够缩短产品的成型周期,并且能够减小设备的锁模力。当塑料成型周期缩短到40%左右时,能够在提升生产效率的同时控制能耗,即保证了整体生产效率的提升又使成本得到了控制;而当注塑设备的锁模能力达到40%左右时,可以降低模具的能耗从而延长其使用寿命。
1.4 技术规范
微发泡产品成型技术规范要求主要体现在对产品壁厚的要求,对材料没有任何要求。壁厚过小或过大都会影响产品功能的正常发挥,所以在制作时要参考设计标准规范对其进行严格控制,使用相应方法达成目标。通常情况下骨位主壁与螺旋壁比值应小于1,注塑比比值应控制在0.6左右。
2. 技术应用于产品生产工作的局限性
此项技术也有其局限性,主要在于它不适用于对外观要求高的产品。单纯使用发泡技术无法保障产品的外观质量,产品外观通常会出现银纹,甚至还可能存在流痕。(如图1所示)
这是由于产品在注塑的过程中,料流前锋没有遇到任何阻力,溶胶发泡进而破裂并被拉长导致的。
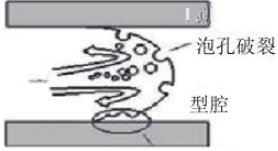
图1 制件表面流痕示意图
3. 解决问题需要的方法
要解决单纯应用发泡工艺可能导致外观出现流痕的局限性,需要将微发泡与反压工艺二者有效结合起来。利用模腔内部存在的反压力来对发泡程度进行控制,可以使内部泡孔密致、强度达到实际需要,从而保证产品的外观质量。反压工艺应用一般是利用压缩气体使模具增压,在实际生产中主要的设备有注塑机和压力控制设备。具体的操作是在熔体注射以及模具填满以前保持一定的反压压力,从而将熔体压向模具表面。同时还要注意时间问题,防止气体压力使制品外观与腔型面接触时间太长,避免由于收缩导致与型腔面脱离。
4. 微发泡+气体反压设计
在设计上首先要考虑的是密封性问题,由于反压模具需要保持一定的压力,所以要将模具密封。为了保障产品外观质量,在模具分型面的设计上要考虑进气要求,确保型腔内部在塑料注料前能够保持一定的压力并使产品表面不存在发泡问题。进气的不均匀会导致产品表面发白,所以在设计上要确保进气均匀。发泡剂的选择作为一项重要工艺参数会对产品质量产生重要影响,如果微孔注射成型要重点考虑发泡剂含量。要保障聚合物中的气体含量符合溶解度要求。发泡剂含量在一定范围内与泡孔的密度成正比,与泡孔的尺寸成反比,泡孔的密度会随着发泡剂含量的增加而增大,尺寸则会相应减小。假如发泡剂含量过大,无法有效溶解于熔体的部分气体会在成核环节首先进入已存在的气相,从而产生大量的气泡,无法达成标准要求。假如发泡剂含量过低或不足,也会使产品在气孔尺寸方面达不到要求。为了确定合理的发泡剂用量,企业需要根据不同的情况多次试验才能得出。为了确保产品内部能够发泡,同时避免产品外部发白,要结合产品壁厚以及型腔压力对其产生的影响来控制发泡剂的应用比例。
要将模具注射的温度控制在合理范围内。因为假如模具注射的温度过高,塑料会降解,同时增大了气泡破裂的可能性,从而使气泡内部气体散逸,降低发泡数量。假如模具注射的温度过低,反过来又会降低发泡的扩散速度。在实际生产过程中,假如物料外观条件允许,而且是在加工温度范围内,适当地采用高温增快液体速度,可以有效缩短产品的生产周期。在模具加工方面,薄壁产品对加工有更高的要求,哪怕是毫米级别的误差也会对产品的生产工作以及产品的性能产生严重影响。相比于常规工具,成型工艺由于对误差更敏感因此具有更高的加工要求。
5. 结语
汽车市场规模及其需求的扩大不仅改善了人们的生活,同时也使汽车技术与工艺得到进一步发展。发泡工艺与反压技术的结合在保留发泡工艺自身优势的同时也避免了单一应用发泡工艺所导致的质量问题。汽车质量以及能耗的降低,使得整体成本得到控制,从而提升了企业的经济效益。
参考文献
[1]唐哲;张亮会;王金锁。抽真空反压技术在化学发泡模上的应用[J].模具制造.2019(10)
[2]卢蒙生.汽车车门内饰板产品微发泡和气体反压工艺介绍[J].科技创新导报.2018(04)
[3]高振海;李明月;高菲;宋学伟;梅兴泰;杨枫;张皓。车用座椅发泡密度对乘坐舒适性的影响分析[J].湖南大学学报(自然科学版)2019(10)
相关热词搜索: