针对传统装煤站装车系统中存在的机械问题,提出自动定量装车系统机械改造方案。从增加自动控制系统、安装碰撞感应装置以及架设排气孔三方面进行阐述。改造后的自动定量装车系统经工业试验,结果表明改造后的装车系统每列车节约时间近54.5min,并且运行安全、稳定。
铁路是煤炭运输的主要方式之一,全国约有60%的煤炭生产运输作业依赖于铁路运输。煤炭装车系统是煤炭铁路运输的主要环节之一,精确且高效率的装车系统既可以增加煤炭公司的利益,又可以确保铁路运输安全高效,有较好的社会效益和经济效益。随着中国经济的快速发展,煤炭运输量也大幅增加,提出了对铁路运输速度,负荷计量准确性,安全生产和人员效率等一系列的更高要求。因此,实现连续、高效、准确的煤炭装载是一个紧迫的问题。目前,大型高速定量自动装车系统已成为实现煤炭铁路高速运输的有效手段,但现有的传统煤炭装车系统采用缓冲仓+定量仓的方法。缓冲仓位于输入罐上方,以消除静态称重,装载和连续装载之间的冲突的方式过于老旧,并且位于计量室上方的缓冲仓的高度越高,整个系统高度越高,增加了装车的安全隐患和装车系统的投资预算。在分析传统装车系统存在问题的基础上,提出定量自动装车系统进行技术方案改造,并基于改造后的自动定量装车系统进行工业试验。
铁路是煤炭运输的主要方式之一,全国约有60%的煤炭生产运输作业依赖于铁路运输。煤炭装车系统是煤炭铁路运输的主要环节之一,精确且高效率的装车系统既可以增加煤炭公司的利益,又可以确保铁路运输安全高效,有较好的社会效益和经济效益。随着中国经济的快速发展,煤炭运输量也大幅增加,提出了对铁路运输速度,负荷计量准确性,安全生产和人员效率等一系列的更高要求。因此,实现连续、高效、准确的煤炭装载是一个紧迫的问题。目前,大型高速定量自动装车系统已成为实现煤炭铁路高速运输的有效手段,但现有的传统煤炭装车系统采用缓冲仓+定量仓的方法。缓冲仓位于输入罐上方,以消除静态称重,装载和连续装载之间的冲突的方式过于老旧,并且位于计量室上方的缓冲仓的高度越高,整个系统高度越高,增加了装车的安全隐患和装车系统的投资预算。在分析传统装车系统存在问题的基础上,提出定量自动装车系统进行技术方案改造,并基于改造后的自动定量装车系统进行工业试验。
1、自动定量装车系统存在的问题
1.1 效率低下、人为误差大
一般煤场的原始系统都是带式输送机的移动装载系统。该系统主要由固定输送带和移动输送带组成。通过规划绞车将车皮运至称量轨道衡,当装载货车运输到轨道秤上的装载点时,由工作人员手动输入仓号。通过向移动输送机发送执行代码,执行装车过程并重复直到整个列车准备就绪。整个装车过程主要需要完成传送带运输,装载系统启动,工作人员进行操作和装载绞车等,需要至少三个工作人员的人工,耗时大约7min。
由于为人工执行装车过程的控制,无法避免相关的误差产生。且需要手动平车来对人工误差进行弥补,因此一旦出现失误,极大地增加装车过程所需要的时间。特别是在进行装车作业时,装载计量是人工设置,人为干预的因素很多,经常有吨位损失产生,导致铁路罚款和业务与客户的纠纷。这样的装车速度严重影响了煤场的运输、装车能力,并大大增加了煤炭生产的核算成本。
1.2 溜槽脱落现象
许多装车站使用的列车型号不统一,多为各类小型货车混合编制。由于型号不同,混合小火车的高度不均匀,因此在装载过程中小火车之间的连接部件可能会断裂,与滑架碰撞导致溜槽坠落。通常需要几个小时才能将脱落的溜槽重新安装,这不仅会导致许多货物延迟运输,而且对铁路部门也会造成非常严重的影响,严重的情况下会影响到列车分配计划的批准。
1.3 滑槽接缝喷煤
当列车装车作业进行时,定量仓中的煤块由装载料斗装载到列车中时,因为整个滑槽处于完全关闭状态并且煤的瞬时流量很大,大量空气被压缩和储存。这极大地影响了滑槽和量化。弹匣下部与接口之间的间隙使得大量的煤尘与压缩空气一起喷射,严重污染了装载车站周围的空气,并且会导致煤尘堵塞装载机的视野和承受偏心载荷等现象。同时,由于压缩空气被喷射会导致在滑槽中产生强烈的负压。在装煤过程中,压缩空气的压力对滑槽产生严重影响非常容易造成严重的装车事故。
1.4 T 型连接器输出端易损
在装车作业期间,缓冲仓内安装有四级闸板,能够对煤块进给量进行控制。这种方法是通过控制缓冲仓的四个闸板按照一定规则开启、关闭来控制给煤量,通过T型连接器的控制元件对这些设备进行控制。T型连接器分别连接电磁阀、网关以及终端电阻,其工作原理如图1所示。PLC控制器控制电磁开关阀,T型连接器通过连接端口发出指令后发送到电磁阀。终端电阻保证了T型连接器与电磁阀之间的通信质量。由于T型连接器安装在气缸的上部,T 型连接器连接到柱子上的电磁阀容易损坏,导致T型连接器不能正确控制电磁阀的开关,影响正常装车。同时,由于 T 型连接器使用精确的测量组件,如若产生故障,不仅更换困难,而且成本非常高昂。
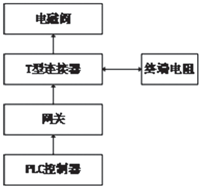
图 1 T 型连接器工作原理
一般煤场的原始系统都是带式输送机的移动装载系统。该系统主要由固定输送带和移动输送带组成。通过规划绞车将车皮运至称量轨道衡,当装载货车运输到轨道秤上的装载点时,由工作人员手动输入仓号。通过向移动输送机发送执行代码,执行装车过程并重复直到整个列车准备就绪。整个装车过程主要需要完成传送带运输,装载系统启动,工作人员进行操作和装载绞车等,需要至少三个工作人员的人工,耗时大约7min。
由于为人工执行装车过程的控制,无法避免相关的误差产生。且需要手动平车来对人工误差进行弥补,因此一旦出现失误,极大地增加装车过程所需要的时间。特别是在进行装车作业时,装载计量是人工设置,人为干预的因素很多,经常有吨位损失产生,导致铁路罚款和业务与客户的纠纷。这样的装车速度严重影响了煤场的运输、装车能力,并大大增加了煤炭生产的核算成本。
1.2 溜槽脱落现象
许多装车站使用的列车型号不统一,多为各类小型货车混合编制。由于型号不同,混合小火车的高度不均匀,因此在装载过程中小火车之间的连接部件可能会断裂,与滑架碰撞导致溜槽坠落。通常需要几个小时才能将脱落的溜槽重新安装,这不仅会导致许多货物延迟运输,而且对铁路部门也会造成非常严重的影响,严重的情况下会影响到列车分配计划的批准。
1.3 滑槽接缝喷煤
当列车装车作业进行时,定量仓中的煤块由装载料斗装载到列车中时,因为整个滑槽处于完全关闭状态并且煤的瞬时流量很大,大量空气被压缩和储存。这极大地影响了滑槽和量化。弹匣下部与接口之间的间隙使得大量的煤尘与压缩空气一起喷射,严重污染了装载车站周围的空气,并且会导致煤尘堵塞装载机的视野和承受偏心载荷等现象。同时,由于压缩空气被喷射会导致在滑槽中产生强烈的负压。在装煤过程中,压缩空气的压力对滑槽产生严重影响非常容易造成严重的装车事故。
1.4 T 型连接器输出端易损
在装车作业期间,缓冲仓内安装有四级闸板,能够对煤块进给量进行控制。这种方法是通过控制缓冲仓的四个闸板按照一定规则开启、关闭来控制给煤量,通过T型连接器的控制元件对这些设备进行控制。T型连接器分别连接电磁阀、网关以及终端电阻,其工作原理如图1所示。PLC控制器控制电磁开关阀,T型连接器通过连接端口发出指令后发送到电磁阀。终端电阻保证了T型连接器与电磁阀之间的通信质量。由于T型连接器安装在气缸的上部,T 型连接器连接到柱子上的电磁阀容易损坏,导致T型连接器不能正确控制电磁阀的开关,影响正常装车。同时,由于 T 型连接器使用精确的测量组件,如若产生故障,不仅更换困难,而且成本非常高昂。
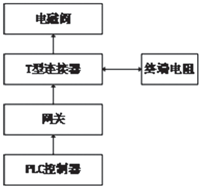
图 1 T 型连接器工作原理
2、自动定量装车系统的改进方案
2.1 应用自动控制系统
为了解决传统的装车误差大、效率低等问题,可以为传统装车系统加装自动控制系统,自动控制系统在装载过程中检测并自动控制从供煤系统到装载系统系统的所有设备,保护装置和检测装置都包含在自动控制系统中。根据装载过程和控制要求,控制系统使用中央控制模式,分为三个部分,即煤炭控制,重量控制和装车控制。在三部分控制中,每个环节都由PLC控制器进行监控。操作模式分为手动和半自动控制模式,可以根据需要和监控过程进行更改,这样提高了装车的精确性,也解决了人为控制效率低下的问题。
2.2 安置碰撞感应装置
通过在滑槽前安装碰撞检测装置解决溜槽脱落问题,控制电路如图2所示(点连接模式而不是边缘连接),K1 始终由接近开关控制闭合,KA1和KA2始终由中间继电器控制,KA1'由KA1和KA2控制。对于由KA2'控制的常开点,K1在正常条件下关闭,KA1充电,KA1'断开且KA2未充电。如果滑槽的高度在提升过程中发生碰撞,感应装置将在与列车碰撞后KA1关闭,KA2'充电,KA2'关闭。控制回路自动提升滑槽,这样就避免了与列车碰撞导致溜槽脱落的发生。
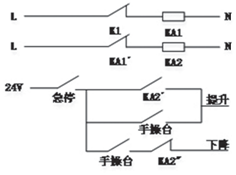
图 2 碰撞感应装置电气原理图
为了解决传统的装车误差大、效率低等问题,可以为传统装车系统加装自动控制系统,自动控制系统在装载过程中检测并自动控制从供煤系统到装载系统系统的所有设备,保护装置和检测装置都包含在自动控制系统中。根据装载过程和控制要求,控制系统使用中央控制模式,分为三个部分,即煤炭控制,重量控制和装车控制。在三部分控制中,每个环节都由PLC控制器进行监控。操作模式分为手动和半自动控制模式,可以根据需要和监控过程进行更改,这样提高了装车的精确性,也解决了人为控制效率低下的问题。
2.2 安置碰撞感应装置
通过在滑槽前安装碰撞检测装置解决溜槽脱落问题,控制电路如图2所示(点连接模式而不是边缘连接),K1 始终由接近开关控制闭合,KA1和KA2始终由中间继电器控制,KA1'由KA1和KA2控制。对于由KA2'控制的常开点,K1在正常条件下关闭,KA1充电,KA1'断开且KA2未充电。如果滑槽的高度在提升过程中发生碰撞,感应装置将在与列车碰撞后KA1关闭,KA2'充电,KA2'关闭。控制回路自动提升滑槽,这样就避免了与列车碰撞导致溜槽脱落的发生。
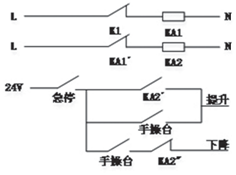
图 2 碰撞感应装置电气原理图
2.3 架设排气孔
为解决喷煤问题,在分流门底部和滑槽顶部添加四个排气口,以便在装载过程中释放瞬间压缩的空气,而不会影响称重仓的称重效果。从排气口中除去压缩的空气,解决了煤尘污染的问题。还可以避免负压的产生,防止滑槽在装载期间被吸入并规避相关事故。
3、使用效果分析
以笔者所在的装车站为例,实施改造措施后,自动定量装车站的装车时间得到了有效的减少,快速装车站最初投入使用时18道单车用时为:4280min(总时间)/598(总车数)=7.16min。改造后18道单车用时为:3100min(总时间)/622(总车数)≈4.98min。整列车节约时间:(7.16min-4.98min)×25车≈54.5min。
通过以上数据对比,快速定量装车站在大部分煤场改造后比改造前单车快2.18min,每列车节约近54.5min,达到了快速定量装车站的设计要求。
4、结语
以选煤厂自动定量装车系统为研究对象,对原有传统装车系统进行改造,以此提高煤炭装车效率和安全,具有一定的先行性。根据目前实际的使用情况,证明上述改造方案是可行的,较好的解决了传统装车系统中存在的问题,同时也为其他煤站应用自动定量装车系统提供了借鉴。
为解决喷煤问题,在分流门底部和滑槽顶部添加四个排气口,以便在装载过程中释放瞬间压缩的空气,而不会影响称重仓的称重效果。从排气口中除去压缩的空气,解决了煤尘污染的问题。还可以避免负压的产生,防止滑槽在装载期间被吸入并规避相关事故。
3、使用效果分析
以笔者所在的装车站为例,实施改造措施后,自动定量装车站的装车时间得到了有效的减少,快速装车站最初投入使用时18道单车用时为:4280min(总时间)/598(总车数)=7.16min。改造后18道单车用时为:3100min(总时间)/622(总车数)≈4.98min。整列车节约时间:(7.16min-4.98min)×25车≈54.5min。
通过以上数据对比,快速定量装车站在大部分煤场改造后比改造前单车快2.18min,每列车节约近54.5min,达到了快速定量装车站的设计要求。
4、结语
以选煤厂自动定量装车系统为研究对象,对原有传统装车系统进行改造,以此提高煤炭装车效率和安全,具有一定的先行性。根据目前实际的使用情况,证明上述改造方案是可行的,较好的解决了传统装车系统中存在的问题,同时也为其他煤站应用自动定量装车系统提供了借鉴。
相关热词搜索: